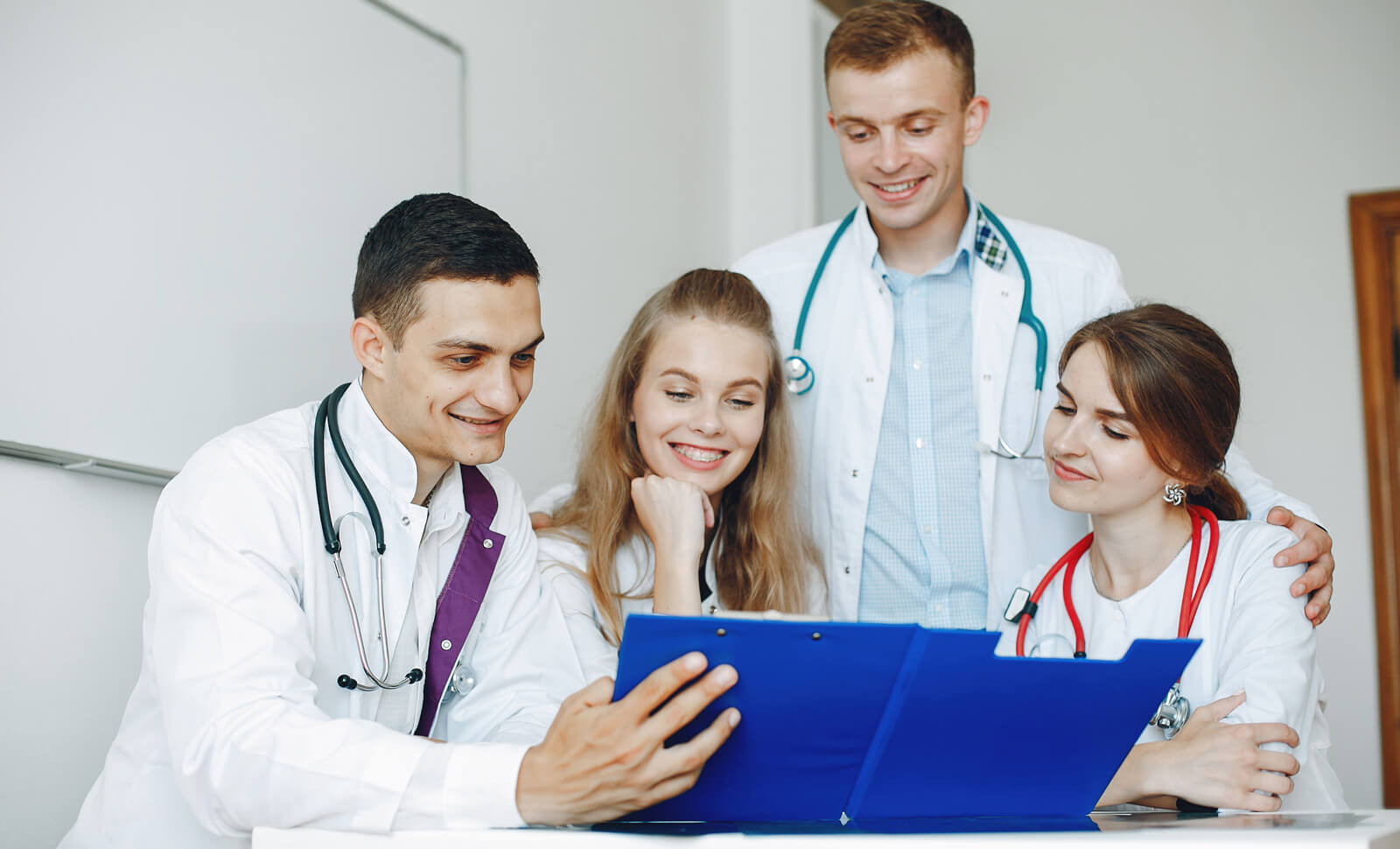
Patricia C. Amedee 4401 Waldeck Street
Grapevine Nashville, TX 76051
(001) 88451234
(001) 88455438
Patricia C. Amedee 4401 Waldeck Street
Grapevine Nashville, TX 76051
(001) 88451234
(001) 88455438
A leading provider of Pressure Area Care Solutions to the NHS and Private
Support caregivers and patients can rely on
A leading provider of Pressure Area Care Solutions to the NHS and Private
Support caregivers and patients can rely on
iQ Medical has an on-
A number of downloads are available of completed studies, that demonstrate our products' performance and effectiveness.
IQ Medical understand how important training and education is to our customers. We can tailor training to meet individual needs as well as providing resources that you can access here such as product training videos, educational content around pressure injuries and knowledge assessments.
Bespoke training can be arranged and delivered to support customers who have invested in our products.